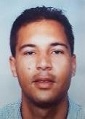
Guy Antou
University of Limoges, France
Title: Instrumentation and numerical modeling of the spark plasma sintering process – application to scale-up
Biography
Biography: Guy Antou
Abstract
The Spark Plasma Sintering (SPS) process can lead to significant temperature and stress gradients within the graphite tools and the powder bed during the densification treatment. The establishment of the temperature and stress fields depends on the geometry of the used tools, the applied uniaxial stress, the considered temperature range and the thermos-physical properties of the sample. The identification of these gradients and the determination of their amplitude are necessary to precisely know the experimental conditions applied to the powder and to evaluate the possible thermomechanical gradients that may appear within the sample, especially in the case of large parts. The thermomechanical conditions seen by the powder bed directly impact the densification mechanisms and, finally, the microstructure and working properties of the sintered bodies.
In this context, the optimization and prediction of the thermo-physical properties of the SPS process depend on reliable numerical models that can simulate the consolidation process. An electro-thermo-mechanical numerical model of the SPS process has thus been developed [1]. Concerning the electrothermal part, the input electrical data of the model were measured experimentally thanks to the development of a specific instrumentation. The main operating characteristics of the pulse generator have been highlighted as well as the effect of pulsed current on Joule heating kinetics at the start of sintering [2]. From a thermomechanical point of view, based on a robust experimental approach to identify powder densification mechanisms [3-4], the constitutive law has been integrated into the numerical model [1].
This approach coupling experimentation and simulation has been applied to the study of scaling-up problems in SPS, considering for example alumina pellets with a diameter greater than 50 mm (Fig. 1). The results of the numerical model have been correlated with microstructural features of the sintered compounds, especially in terms of spatial distribution of relative density.
Fig. 1. Calculated temperature distribution throughout the complete die/punches/powder set-up at the end of the isothermal stage (t=1470s).
Recent Publications
1. Diatta J, Antou G, Pradeilles N, Maître A (2017) Numerical modeling of spark plasma sintering—Discussion on densification mechanism identification and generated porosity gradients. J Eur Ceram Soc 37:4849-4860.
2. Diatta J, Antou G, Courreges F, Georges M, Pradeilles N, Maître A (2017) Effect of the current pulse pattern during heating in a spark plasma sintering device: Experimental and numerical modeling approaches. J Mater Proc Tech 246:93-101.
3. Antou G, Guyot P, Pradeilles N, Maître A (2015) Identification of densification mechanisms of pressure-assisted sintering: Application to hot pressing and spark plasma sintering of alumina. J Mater Sci 50:2327-2336.
4. Antou G, Guyot P, Pradeilles N, Maître A (2015) New Approach of the Evolution of Densification Mechanisms During Spark Plasma Sintering: Application to Zirconium (Oxy-)Carbide Ceramics. Scr Mater 101:103-106.
5. Kozak K, Dosi A, Bucko M, Chlubny L, Lis J, Antou G, Chotard T (2017) Investigation of the mechanical behavior of MAX phases by acoustic emission technique. Mater Sci Eng A 707:73-80.